MVEC Celebrates 90 Years: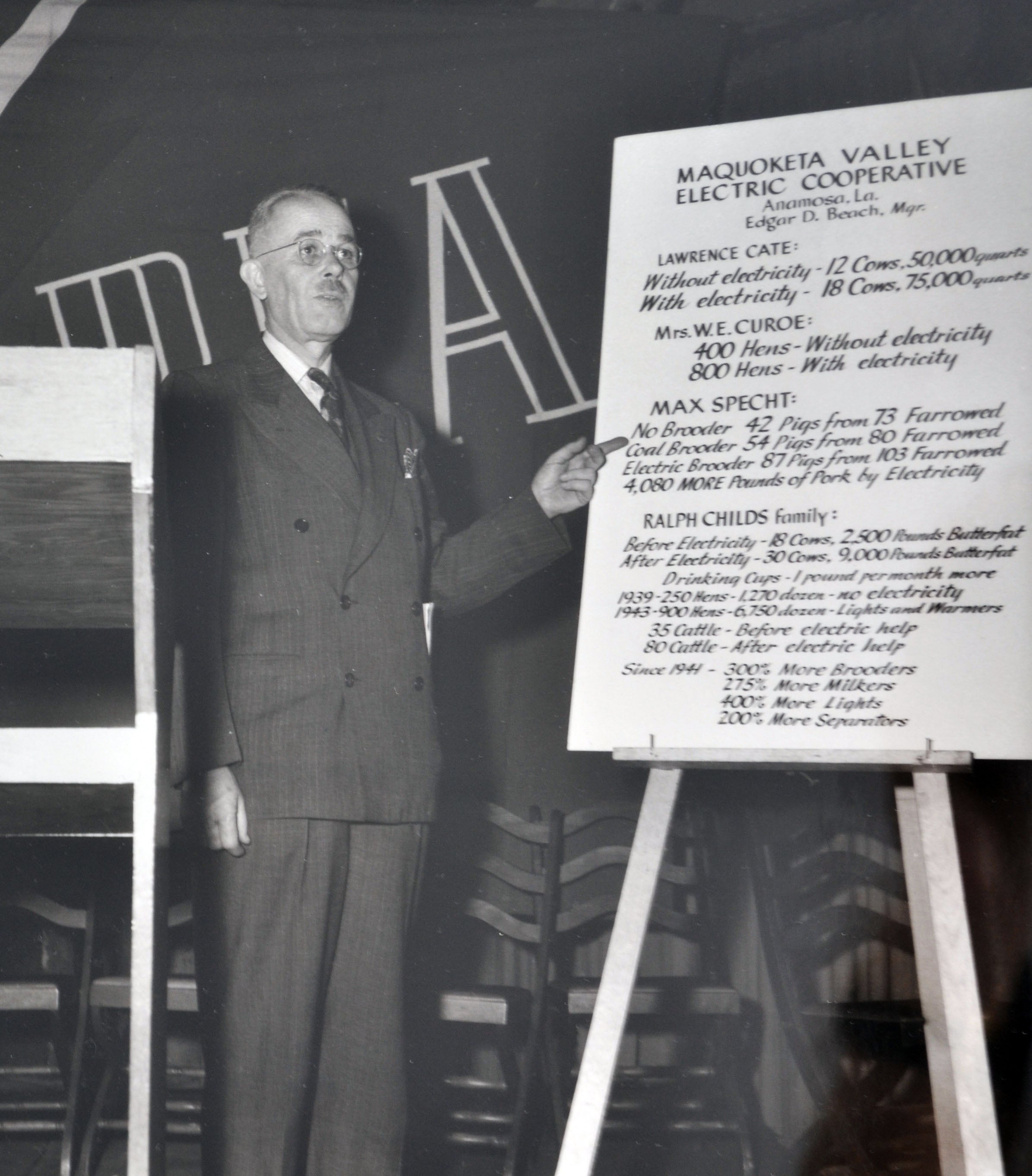
How it All Began
MVEC is celebrating its 90th anniversary in 2025.
To commemorate this milestone, in each Watts Current newsletter, we will share a fun fact, throwback photo, or a bit of co-op history.
In today’s increasingly digital and electrified world, it is hard to imagine life without power at the flip of a switch. But, until the mid-1930s, rural eastern Iowa functioned without electricity. Did you know that MVEC came about because of a local county agent, Carl Smith, who pulled together 16 farmers from each of the Jones County townships to form what is now Maquoketa Valley Electric Cooperative? According to an article by late MVEC freelance writer Grace Zimmerman, each person was tasked with contacting their neighbors to join them in ‘throwing in $10.00’ to start a Jones County rural electric cooperative. The goal was to use the funds to attract a loan from the Rural Electrification Administration. While $10 does not seem like a lot today, in 1935, farmers were just coming off the Great Depression where cattle was selling for $15 and hogs for $9 a head. The cooperative was formed in 1935, and in April 1936, Edgar Beach was hired as the first manager. Per Zimmerman’s article, W.B. Meeks was elected as the Board’s first president in 1937.
MVEC’s Board of Directors called a special Board meeting on April 3, 1937 to vote on applying for a loan of $305,000 from the federal government to kick off construction of MVEC’s initial power lines. The cost to build a mile of line in 1937 was $959/mile compared to $140,000/mile today. MVEC’s initial electric rate was $.04 cents per kWh up to 119 kWh used per month (today’s rate is $.172 kWh for on-peak and $.084 for off peak usage). The average member bill in 1938 was $4.07. The first MVEC member to receive power was E.M. Scott who lived about a mile south of Baldwin in Jackson County. MVEC originally got its power from Maquoketa Municipal power plant, hence the name Maquoketa Valley Electric Cooperative.